A PANEL OF EXPERTS ANSWER DRYCLEANERS’ QUESTIONS ABOUT BUYING OR SELLING A POTENTIALLY CONTAMINATED PROPERTY AND THE COMPLEX ENVIRONMENTAL AND LEGAL ASPECTS THAT SHOULD BE CONSIDERED
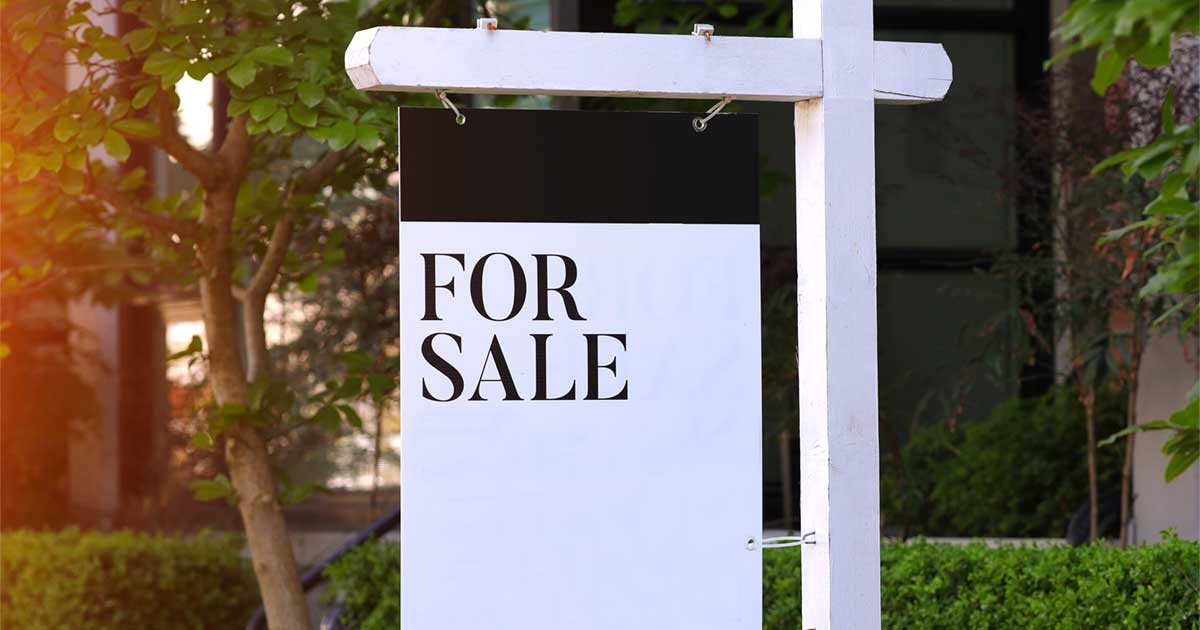
The purchase or sale of a drycleaner property and business is a delicate dance between the parties involved because of the potential discovery of PCE contamination and other environmental liabilities during the due diligence process. Luckily, there are options available to both buyer and seller to keep a deal from falling through. First, you need to enlist a trusted environmental professional to assess areas of concern properly. Second, you need to hire an experienced environmental attorney to shepherd the negotiation through the proper legal mechanisms, environmental liability, purchase of the business or the property itself, as well as utilizing insurance assets to bargain for a fair deal.
At a National Clothesline webinar, EnviroForensics, PolicyFind, and Scarinci Hollenbeck discussed how to buy or sell a drycleaner. At the end, attendees submitted their questions for the panel to answer.
Watch the recording of the webinar, “Why Phase I ESAs are Important for Buying or Selling a Drycleaner.”
This Q&A session has been lightly edited for clarity.
WHAT HAPPENS IF CONTAMINATION IS FOUND DURING DUE DILIGENCE? DOES THAT MEAN I CAN’T SELL?
JOHN SCAGNELLI: No, it doesn’t mean you can’t sell. It basically means that the extent of that contamination needs to be understood and determined, and the cost to remediate should be estimated. Once you’ve done that, both parties can either agree to an adjustment to the purchase price with either the buyer or the seller addressing the liability before closing, or the seller can accept responsibility and remediate the contamination after the closing. So, no. Finding contamination during due diligence does not mean you can’t sell the property. It means that you have to adjust the parameters of the sales transaction to take that contamination into account.
JEFF CARNAHAN: The bottom line is you’re going to have to face the possibility that there could be impacts and you need to be willing to devise a plan to deal with that liability in order to get the deal done. In my experience, it’s sort of like playing hot potato with that liability and seeing where it lands.
DAVID HOFFMAN: In order to do what John suggested you need to utilize an environmental consultant that can vet costs and cost parameters to whatever the condition or problem might be, and you would need to use an attorney that is capable of handling a transaction that has an environmental aspect to it. An attorney with environmental experience can properly set up the transaction in escrow perhaps or use any other mechanisms at their disposal so that the transaction can go forward.
Learn how to sell a drycleaning business in three steps
HOW MUCH DOES A PHASE I ESA COST?
DAVID: Phase I Site Assessments are site-specific and they can vary and change depending on the length of time the business was there and the size of the property. So they can vary between $1,500 to $4,000 depending on the property. For example, a single building retail site would fall in the middle of that range.
JEFF: I’d add that Phase I Environmental Site Assessments can be considered commodity work by buyers and sellers and by lending institutions. A lot of times, they’ll see a Phase I as just checking a box because in the world of buying and selling across most industries. Environmental contamination is not an everyday situation. But, with drycleaners it definitely should be anticipated. The reason I bring that up is to warn you to be cautious when looking for the lowest-cost provider. When you’re talking about this much liability, don’t let that responsibility fall into the hands of the lowest-cost provider. Choose your team based on skills and capabilities and past experience.
Find out the 5 considerations when selecting an environmental consultant
HAVE THERE BEEN CONTAMINATION CASES FOUND AT DRYCLEANERS USING HYDROCARBON SOLVENTS?
DAVID: Yes, but normally the contamination issue that they’re finding is PCE. I would note that hydrocarbon solvents are an environmental contaminant as well, which is why I would recommend conducting the industrial process of your drycleaning plant the same way that you would if it was PCE; have the waste handled by a licensed hauler and document that, so that in the future when someone does the Phase I on a hydrocarbon plant there won’t be any surprises. A lot of the alternative solvent manufacturers are branding and advertising their alternative solvent as “environmentally friendly”, and while it is “environmentally friend-lier” it still can potentially be a contaminant to the environment.
JOHN: Just to add to that, we haven’t seen any court cases with respect to hydrocarbon contamination relating to drycleaners, but the point that David made is correct. Hydrocarbons would still be a contaminant for purposes of many environmental statutes at the state level and would still be considered ultrahazardous activities for purposes of liability in common law. So you’re still going to have to properly manage your use and handling of hydrocarbon-based solvents. If you went outside your back door and threw it outside on the ground it would be considered a “discharge” in virtually all states. We’ll probably start seeing some legal cases about this as PCE is being phased out. You’re still going to have the same concern to handle it and manage it properly, and you’re still going to have to evaluate whether there’s any contamination as part of your due diligence process during real estate transactions.
DAVID: Prior to the existence of safety clean and waste handlers in 1986-1987, drycleaners would put their PCE waste into the dumpster. Since the dumpster normally stayed put, the area around the dumpster outside of a drycleaner is often considered a Recognized Environmental Condition (REC). Like PCE pre-1986, there’s a potential for drycleaners to consider hydrocarbon waste nonhazardous, and put it in the dumpster. If that hydrocarbon leaks out of the dumpster, and in the future hydrocarbon is regulated like PCE is today, we would have a retroactive liability where we’re assessing hydrocarbon contamination beneath dumpsters. So, again, the waste handling procedure for hydrocarbons is just as important as PCE.
WHAT PERCENTAGE OF YOUR PHASE I STUDIES OF DRYCLEANERS LEAD TO A PHASE II?
DAVID: My answer would be most. The reasons being that most drycleaners have been there for a while, we have the REC of the dry cleaning machine, the industrial process of handling the chemistry, the operation of the still, and the waste storage area which is where the safety clean containers are. These are all RECs that require testing and sampling in a Phase II. If we’re talking about a drop store that’s always been a drop store, then those RECs I just mentioned don’t exist.
JEFF: I’d agree with that David, and I wouldn’t just say “most” I’d go one step further and say “most plus.” In my experience, the mere presence of a drycleaner will cause many small business administration lenders to ask for a Phase II despite what the operational history in the databases may show.
DAVID: The other important thing is that in order to gain the protection and be successful in this process, the environmental professional actually has to look for the contamination and make a diligent effort to find it. The Phase I on the drycleaner that says “no further action” might seem like a good thing on the surface, but without a diligent effort to find environmental contamination, it could create a hodgepodge of legal problems in the future.
IS CONTAMINATION ORIGINATING FROM WASTEWATER (SEPARATOR WATER) MANAGEMENT MORE COMMON THAN LARGER SPILLS?
JEFF: Overall, there have only been a few drycleaners that we’ve worked with that have had recorded larger spills. Very few situations where they said ,”Oh my gosh! We know that we dumped a drum” or “the delivery driver accidentally dragged a hose across the driveway,” but most of the time it’s a series of incidental releases that go unseen and unknown for years that caused the problems.
DAVID: In the past, the separator water has been an issue that has caused environmental contamination to the site, especially when you combine the older plant that discharged the separator water directly to the sewer, and the sewer being in the form of a septic tank. We see a lot of discharges at septic tanks that are related most likely to the separator water more than to the handling of pure PCE at the plant. I’d add that the conventional sewer lines that go to the municipal sewer are not built to contain the chemistry and ensure that every drop of it doesn’t leak on its route to the sewer plant. So, even if you have a municipal sewer, you can end up with PCE in the ground at the poorly fitted joints in the sewer system.
20 YEARS AFTER A DRY CLEANER HAS LEFT THE LOCATION WOULD A PHASE I LIKELY IDENTIFY THE OLD DRYCLEANERS’ EXISTENCE?
DAVID: The answer is yes because the Phase I does a historical search of the site, the location, and all the prior uses going back to when the site was vegetative in order to meet the requirement. Some of the insurance maps that were drawn long ago still exist and they go back to the 1890’s.
JOHN: Another implication of this question would be “is it possible to go back after the drycleaner who was on the property 20 years ago for cost recovery for remediation of environmental contamination?” If you’re seeking cost recovery against that drycleaner for cleaning up that contamination 20 years after it left the property, you have to have some proof linking that drycleaner to discharges relating to its operations.
ARE PHASE II SURVEYS COSTLY?
JOHN: The cost of doing a Phase II is a function of what parts of the property were identified as areas of concern during the Phase I and the different media (soil, groundwater, soil gas, etc.) you are investigating, so your cost will be variable based on those factors. You want to make sure that your environmental professional follows the Phase I results and delineates areas that are suggested by the Phase I results. You want to go as narrowly as possible to accomplish the objective. That said, it’s very difficult to provide any estimate of cost.
JEFF: To add to John’s point about starting as narrowly as possible, that’s the key. It’s not just “go out and make a science project of this property,” it’s “look at those areas that the Phase I has identified, and hone in on those areas. And, John’s right about the costs of a Phase II varying. That said, I’m personally comfortable saying that a Phase II can range between $15,000 to $25,000.
DAVID: The reason there’s such a spread is that no one can know the breadth of a Phase II without the results of a Phase I. I would be very suspicious of any Phase II estimate that is given to a client before a Phase I is complete.
IF I’M RENTING AND DON’T OWN THE PROPERTY, WILL MY INSURANCE STILL PAY FOR CLEANUP?
KRISTEN: It depends on when you rented and when you had coverage. If we look back and find historical policies dating back to the mid-eighties or so, and if you had a business owners policy that had a general liability coverage part, absolutely! If you had Pollution Legal Liability (PLL) policies, those can be of use as well.
JOHN: A little more about PLL policies. These are specialty policies that are taken out if you’re an operating drycleaning business, and they may provide you with both cost of response payment for remediating releases and the defense from liability in third-party legal action. This type of policy is available to property owners as well as renters.
Learn how old CGL policies can help offset environmental cleanup and legal defense costs
IS IT POSSIBLE I DON’T HAVE PERC CONTAMINATION?
JEFF: It really depends on how long your operation was in existence. Do business operations at that location go all the way back to transfer machines? Is it only 10 years old or 30 years old? Was it a Stoddard operation for a while and then transferred to PERC and then back to a different solvent? In EnviroForensics’ experience working with drycleaners, I’d estimate that only 10% ended up having zero contamination.
IF I START THE INVESTIGATION AND CLEANUP PROCESS CAN I SELL MY PROPERTY IN THE MIDDLE OF THAT PROCESS?
JOHN: The answer is yes, you can. If you’re doing a remediation, you’ll likely have your environmental state agency involved in that process and there are provisions in many statutes and administrative agency regulations which would provide for the transfer of titles with permit transfer of title to a property to another party during the remediation process. You might have to post remediation of a bond or an escrow amount relating to it or sign remediation certification of transfer responsibility. Your attorney handling the transaction will have to be familiar with the environmental requirements of the state in which your property’s located and comply with those.
Learn more about how we can assist in the real estate transactions of drycleaners and other potentially contaminated properties