TIPS FOR DRCLEANERS FROM A DECOMMISSIONING EXPERT
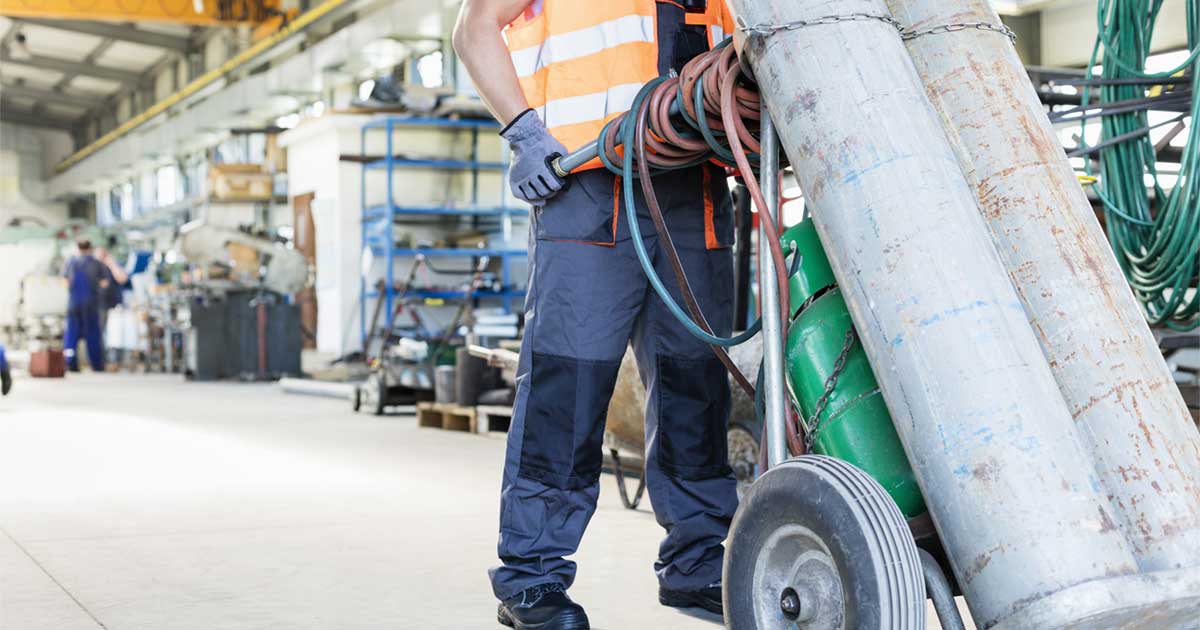
BY: JEFF CARNAHAN AND JEFF DUNN
Keeping in step with recent articles related to hot topics of the day, this month I decided to reach out to a friend who knows the ins and outs of decommissioning a drycleaning plant. Jeff Dunn with Machinex in Cincinnati, Ohio will talk us through the process, and I’ll add-in some commentary about environmental things to be aware of.
UNDER WHAT CIRCUMSTANCES DO DRYCLEANERS DECOMMISSION THEIR PLANTS?
JEFF DUNN: Changes in business, the economy and in your life can lead you to consider decommissioning your drycleaning facility. Be it planned retirement, downturns due to COVID-19, new opportunities, slow business, or the need for a larger place due to expanding business, putting together a plan to decommission your plant is important. Knowing what to expect and what to plan for will save you time and money.
HOW MUCH DOES IT COST TO DECOMMISION A DRYCLEANING PLANT?
DUNN: Each situation and every store is different so the cost to have this work done by a third party will vary from $1,000 to $25,000 or more depending on the scope of work, location and size of the facility, the number of pieces of equipment and the solvent. If you have the technical skill to do certain things, you can bring in service technicians, distributors or riggers to do specific portions of the decommissioning and reduce the overall cost.
WHAT IS THE PROCESS FOR DECOMMISSIONING A DRYCLEANING PLANT?
DUNN: There are three primary elements involved in a plant shutdown:
- Landlord & Lease Concerns
- Equipment: Disconnecting/Removal/Disposal
- Safe Chemical and Solvent Disposal
STEP 1: YOUR LANDLORD AND LEASE
Unless you own a free standing building you will first have to coordinate a plant decommission with your landlord. Coordinate with the landlord on the timing of the shutdown and the precise conditions they have stipulated the space to be in. Most of this will be covered in your lease so carefully reviewing the lease conditions and expectations of the landlord will be the first step in insuring a smooth departure free of legal ramifications.
JEFF CARNAHAN: EnviroForensics and the law firm Davis Kuelthau in Milwaukee gave a recent webinar on How to Terminate or Renegotiate Leases for Dry Cleaners. The recording is available on our website. Check it out.
STEP 2: EQUIPMENT REMOVAL / DISPOSAL
DUNN: You will be responsible for removal of all equipment. If there is a residual value to your equipment this will have a big impact on your planning and the time required to vacate the premises.
Be prudent when valuing your equipment if you plan to sell it. Due to economy, many cleaners have closed, and others are reducing their footprint. This means that there are plenty of pieces of good used equipment on the market. So be honest with yourself, anything with 15 or 20 years of age will be of little value despite the wonderful years of service it has provided and the impeccable condition in which you have maintained it. In most cases what you think it’s worth is at least twice as much as reality. You also have to factor in timing. If you have to be out in 30 days, you should price it aggressively otherwise you may still have it and either have to move it to storage or junk it.
Basic questions of logistics apply for equipment removal:
- Do you have door openings large enough for the largest piece of equipment to come out?
- If not, do you have windows or doors that can be removed to get equipment out?
- Will you need to have windows removed and for how long? Can I secure the store for long enough with windows/doors removed to get the equipment out?
- Is there adequate room in the parking lot to remove and stage the equipment as it comes out?
- Do you need to coordinate the time and parking space needs with the landlord?
- Do you have a licensed electrician or knowledgeable technician available to disconnect the electrical from your equipment and safely secure and or remove the wiring back to the electrical panel?
Drycleaning Machines
Preparation is particularly important if your drycleaning machine solvent is perchloroethylene (Perc), due to its hazardous nature. But other solvents should also be handled in a safe manner. All solvent, waste, carbon and filtration should be removed from the machine. Transporting a drycleaning machine with any solvent in it is not recommended and certainly not with perc which would be illegal.
CARNAHAN: Here is where things have the possibility of going wrong from an environmental standpoint. I have seen contamination issues resulting from improperly transferred or stored Perc during decommissioning. It is a hazardous waste and must be managed as such, by law, as JD mentions. I’ve also seen empty drycleaner spaces with drums of solvent left behind after the operator left town. This is a dangerous situation because an empty store invites trouble. I was involved in a case once where someone broke into an empty, decommissioned drycleaner store with drums of waste Perc left inside and they turned them all over for fun. Guess who got the blame and had the ultimate responsibility for that?
DUNN: If the drycleaning machine is to be resold, there is a long list of things that need to be done before the boiler, the air compressor or the electric is shut off. There isn’t room to go into that topic here but contact Mechanix and we’d be glad to share it.
If you are going to dispose of the drycleaning machine, most scrap metal companies will want to see a clean dry machine with all tanks and doors open, filters and carbon removed, and refrigerant lines cut (following removal of the refrigerant).
CARNAHAN: If residual solvent is left in the machine and a scrap metal company accepts it, you may not yet be off the hook. If you aren’t the only person they took dirty equipment from, they could have a contamination problem of their own. It is common at regulated cleanup sites like scrap metal processors and landfills, for the regulatory agency to demand a list of all their customers. With this list, the agency starts making demands for a portion of the cleanup costs.
DUNN: Chillers
Chillers can also require special handling depending on their configuration. You may need to evacuate the chiller of refrigerant in a similar manner to the drycleaning machine.
Boilers
Depending on the age of your boiler, you may have mercury switches in the boiler which, if disposing of the boiler, will have to be removed and handled separately. States and municipalities have different ways of handling mercury disposal so it’s best to get in touch with your local Environmental Quality authorities.
CARNAHAN: Note that mercury switches are also considered a listed waste by the US EPA and must be disposed of at a designated facility. Usually, they can be dropped off at a local hazardous materials collection center. Most towns have at least one.
DUNN: Presses & Finishing Equipment
Consider leaving the air on to assist in preparing presses for removal. If presses are being sold and/or shipped it is sometimes a good idea to have a qualified technician close the pressing head while the compressed air is on and then block the head closed for safer and easier transport.
Also, the compressed air can be used to assist in blowing lint and dust out the facility. Consequently, my recommendation is to keep the air compressor and the electricity on until the very end.
General Preparation and Safety
Prepping for equipment removal by making sure machines are disconnected from anchors, placed on wooden blocks when possible and prepared for quick removal is essential if you are paying a rigger or distributor to remove the equipment.
Moving heavy equipment is dangerous. In addition to having the proper knowledge of weight distribution, center points and how and where to lift, having the experience, right equipment and tooling as well as pallets, straps, chains, shrink wrap and proper packaging is very important and best left to professionals.
Valuing Your Equipment
Selling equipment to a distributor or reseller will make scheduling of your departure easier as they will decommission and remove and then store the equipment while awaiting the prospective buyer. All of these things take money and involve risk so don’t expect them to offer you what the going retail price for used equipment is. Selling to an end user direct may net you more money but there is more work and risk involved.
STEP 3: SAFE CHEMICAL DISPOSAL
Know your spotting chemicals, check your Material Safety Data Sheets (MSDS) sheets for proper handling and disposal. Use resources like EnviroForensics and your local distributor to handle this the proper way. In many cases, properly packaged spotting agents and detergents can be given or sold to other drycleaners in the area.
CARNAHAN: I want to thank Jeff Dunn with Machinex for talking with us about decommissioning a drycleaning plant. I can’t stress how important proper solvent and chemical handling is during this process. There have been many instances where spills occur, or disregarded regulations cause lasting environmental liabilities. Nobody needs the capstone event at a closed and decommissioned drycleaning plant to be a contamination incident. Please contact a trusted advisor if you have questions.
Have questions about environmental concerns that may pop up during decommissioning? Contact us today.
As seen in Cleaner & Launderer
Jeff Carnahan, President
Jeff Carnahan, LPG, has 20+ years of environmental consulting and remediation experience. His technical expertise focuses on the investigation and interpretation of subsurface releases of hazardous substances for the purpose of evaluating and controlling the risk and cost implications. He has been a partner of the drycleaning industry for the past decade and is a frequent contributor to the national drycleaning publication Cleaner & Launderer. He is an industry leader in understanding that environmental risk includes not only cleanup costs, but also known and unknown third-party liability.
Jeff Dunn, Owner, Machinex
Jeff Dunn has 30 years of experience in the drycleaning industry. He specializes in Equipment sales, Facility design and Analysis, Parts Supply, and Business Consulting. Dunn owns and operates Laundry and Dry Cleaning Equipment Distributor, Machinex in Cincinnati, Ohio.